Achieving Mirror-Like Finishes With The Mrf Polishing Process
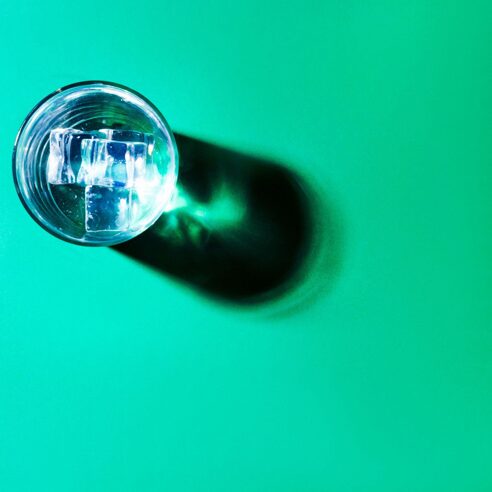
When it comes to precision polishing, few techniques can match the effectiveness of Magnetorheological Finishing (MRF). Whether you’re working with high-performance optics, semiconductors, or precision engineering components, achieving a flawless, mirror-like surface is crucial. The MRF polishing process is a revolutionary method that brings unmatched accuracy, smoothness, and defect-free finishes to even the most delicate materials.
In this article, we’ll explore what makes MRF polishing so special, how it works, and why industries around the world rely on it for ultra-smooth, high-precision surfaces.
Why MRF Polishing Stands Out
So, what makes the MRF polishing process superior to traditional techniques? Let’s break it down:
1. Unmatched Precision
MRF polishing is used in industries where accuracy down to the nanometer level is required. Traditional polishing methods, such as lapping or chemical polishing, often struggle to achieve such a fine finish. However, MRF can polish surfaces with near-zero defects, ensuring absolute precision.
2. Damage-Free Polishing
One of the biggest challenges in polishing delicate materials—such as optical lenses, glass, and high-end semiconductors—is avoiding surface stress or micro-scratches. Since MRF polishing is a fluid-based process, it gently removes material without causing mechanical stress or deformation.
3. Consistency and Repeatability
Traditional polishing methods often require manual adjustments, leading to inconsistencies between different batches. The MRF polishing process, however, is highly controlled and automated. This means that every piece polished using MRF will have the same high level of quality and consistency, making it an ideal choice for mass production in high-tech industries.
4. Versatility in Materials
From glass and ceramics to metals and composites, MRF polishing can be applied to a wide range of materials. This adaptability is one of the reasons why it’s the preferred choice for manufacturers producing advanced optical components, aerospace parts, and semiconductor wafers.
5. Ability to Correct Surface Errors
One of the most fascinating aspects of MRF polishing is its ability to correct optical distortions and other surface imperfections with extreme accuracy. Using computer-controlled feedback systems, the process can identify and remove high and low spots, ensuring a perfectly even surface.
Industries That Benefit from MRF Polishing
The mrf polishing method has transformed surface finishing in several high-tech industries. Here are a few key sectors that rely on this cutting-edge technology:
✅ Optical Industry – High-precision lenses, mirrors, and telescopes require flawless surfaces to ensure optimal performance. MRF is widely used in the production of astronomical optics, microscopes, and high-end camera lenses.
✅ Semiconductor Manufacturing – The semiconductor industry demands surfaces that are smooth at the atomic level. MRF polishing ensures that wafers and microchips meet these strict quality standards.
✅ Aerospace & Defense – From satellite mirrors to advanced weapon systems, MRF plays a critical role in ensuring that optical and metal components function with precision.
✅ Medical Equipment – High-quality medical imaging devices, such as endoscopes and laser systems, require polished surfaces free from any distortions. MRF helps create crystal-clear optics for accurate diagnostics.
✅ Luxury & Watchmaking – Premium watches and luxury glass products often require mirror-like surfaces. MRF polishing ensures these items maintain their pristine aesthetic while enhancing durability.
Final Thoughts
If your industry demands flawless, high-precision surfaces, the MRF polishing process is the gold standard. Its ability to deliver mirror-like finishes with minimal waste, extreme accuracy, and zero mechanical damage makes it an indispensable tool in modern manufacturing.
From high-end optical lenses to advanced semiconductors, MRF polishing is setting new benchmarks for surface perfection. As technology continues to advance, we can expect even greater improvements in this revolutionary polishing method.
So, the next time you admire the clarity of a telescope lens, the smoothness of a high-tech semiconductor, or the brilliance of a luxury watch, remember—MRF polishing might be the secret behind its perfection.